Rust Preventive Oils and Preservatives
Example 1
- User
- Automotive parts manufacturer
- Application
- Automation of rust preventive oil application process
- Model used
- ST-6-1.0X
Problem
This manufacturer produces small automotive parts. After press molding, the products are coated with rust preventive oil. In the past, the products were stored in a bag, and rust preventive oil was sprayed with a mist into the bag, and then the bag was massaged to spread the oil over all of the parts. Since the bag contained several hundred parts and its weight placed a burden on the workers, the customer considered automating the process.
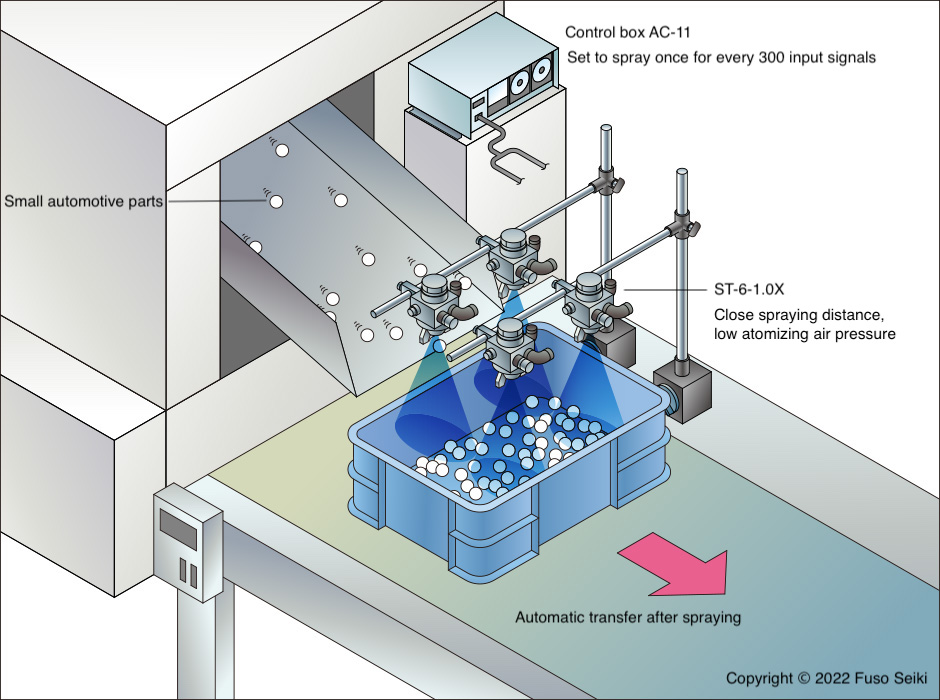
Lumina’s proposal and result
For this project, we used four standard Lumina ST-6-1.0Xs. First, products formed by the press roll down a chute on the side of the machine and are stored in a plastic container. Once 300 products have been collected, the spray guns automatically apply rust preventive oil, which is controlled by an AC-11 control box. The control box can be set to spray once every 300 press input signals.
A key point was to be able to spray without scattering and contaminating the surrounding area as the rust preventive oil used is volatile. Here, the spraying distance was set close, and the atomizing air pressure was lowered to its very limit. Under these conditions, the spray pattern width per gun would be small, so we used four spray guns to cover the entire container.
- (Spraying conditions)
-
- Atomizing air pressure: 0.02 MPa
- Liquid pressure: 0.1 MPa
- Target distance: 130 mm
As a result, we succeeded in automating the rust preventive oil application process. After spraying, a conveyor belt operates to automatically transport the container, completely automating the entire process. This freed workers from heavy labor. Careful setting of spray conditions also minimized scattering.
Example 2
- User
- Manufacturer of steel plates for construction
- Application
- Rust prevention
- Model used
- ST-6R-0.5X
Problem
On a type of construction material called a flat deck that is used in the floors of buildings, the sections that touch concrete are prone to rust and require rust prevention treatment. This manufacturer had previously been using a spraying device for rust prevention treatment, but they were unable to coat only the protruding portions created by press working (which were 36 mm wide). Also, mist overspray was causing their production site to get dirty.
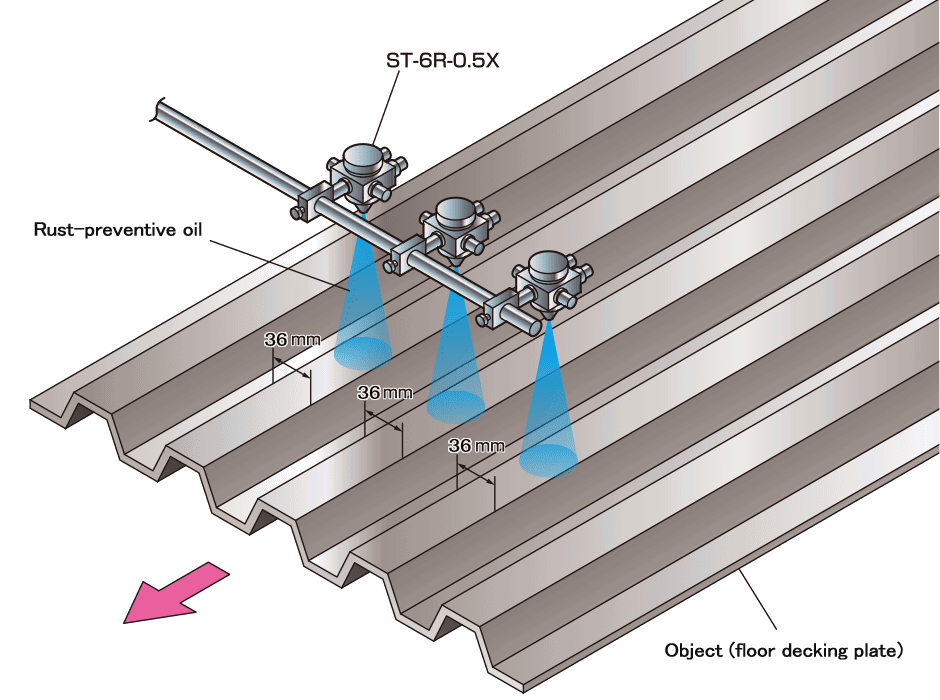
Lumina’s proposal and result
We proposed Lumina’s standard round pattern spray gun, the ST-6R. One ST-6R was installed at each of three points in line with the protruding portions of the flat decks as they were conveyed past. In order to prevent the spray from growing wider than 36 mm, we suggested a close target distance of 20 mm and a low amount of liquid.
- (Spraying conditions)
-
- Atomizing air pressure: 0.03 MPa
- Target distance: 20 mm
- Liquid supply: Gravity feed container
As a result, we provided a system that effectively coated only the protruding portions of the flat decks with rust preventive oil.
Also, the extremely small atomizing air pressure of just 0.03 MPa provided a soft mist of very large droplets that coated delicately and eliminated overspray.
Example 3
- User
- Major lumber factory
- Application
- Providing coatings of anti-mold agent
- Model used
- ST-6-2.0X
Problem
This manufacturer makes wooden spools for electric power and communications cables. They had previously been coating the lumber with anti-mold agent manually, using rollers. In order to decrease employee workload and increase productivity, they needed to automate that process.
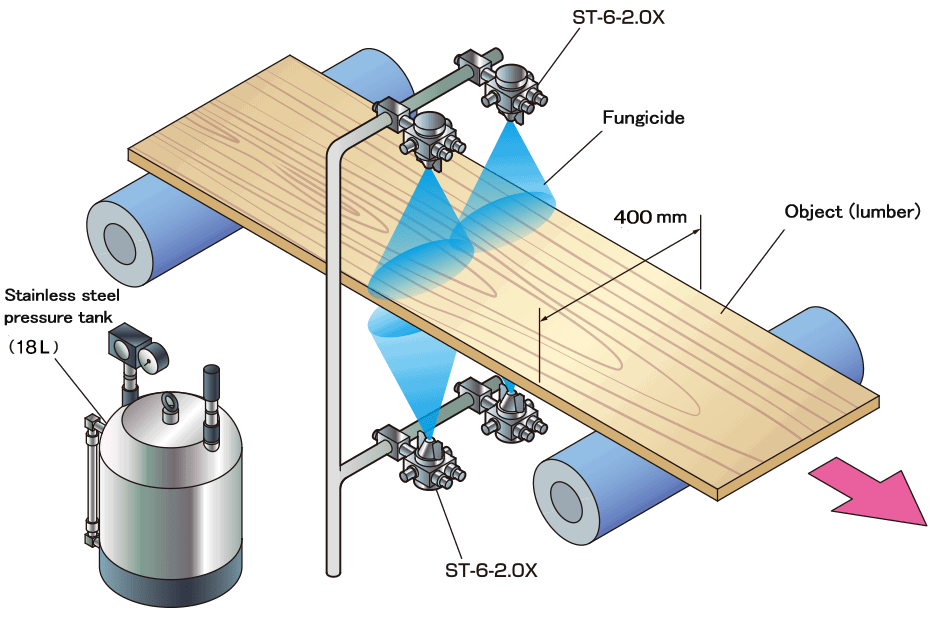
Lumina’s proposal and result
We proposed Lumina’s standard flat-fan pattern spray gun, the ST-6. They wanted to coat with a large amount of liquid, so we recommended the maximum nozzle size, 2 mm . They installed two spray guns on bottom and two on top. The four spray guns completely coated both sides of the 400 mm wide lumber with anti-mold agent as it was being conveyed past them on a belt.
- (Spraying conditions)
-
- Atomizing air pressure: 0.05 MPa
- Liquid pressure: 0.05 MPa (using 18 L pressure feed tank)
- Target distance: 300 mm
As a result, their employees no longer had to coat the lumber manually, greatly improving work efficiently. Also, by setting the atomizing air pressure low at 0.05 MPa, we created a soft mist that did not cause overspray.
This improved coating efficiency, decreasing the amount of anti-mold agent used.