Adhesives and Glues
Example 1
- User
- Automotive parts manufacturer
- Application
- Application of thread-locking adhesive
- Model used
- ST-10-TC8R-1.1X-150L-90
Problem
This manufacturer received a new order to produce automotive anti-vibration rubber mounts. An adhesive is applied to the inside of the hole before inserting a bolt into the hole of the rubber part. The manufacturer was looking for a nozzle that could be used to apply adhesive to the inside of a hole 30 mm in diameter and 40 mm deep.
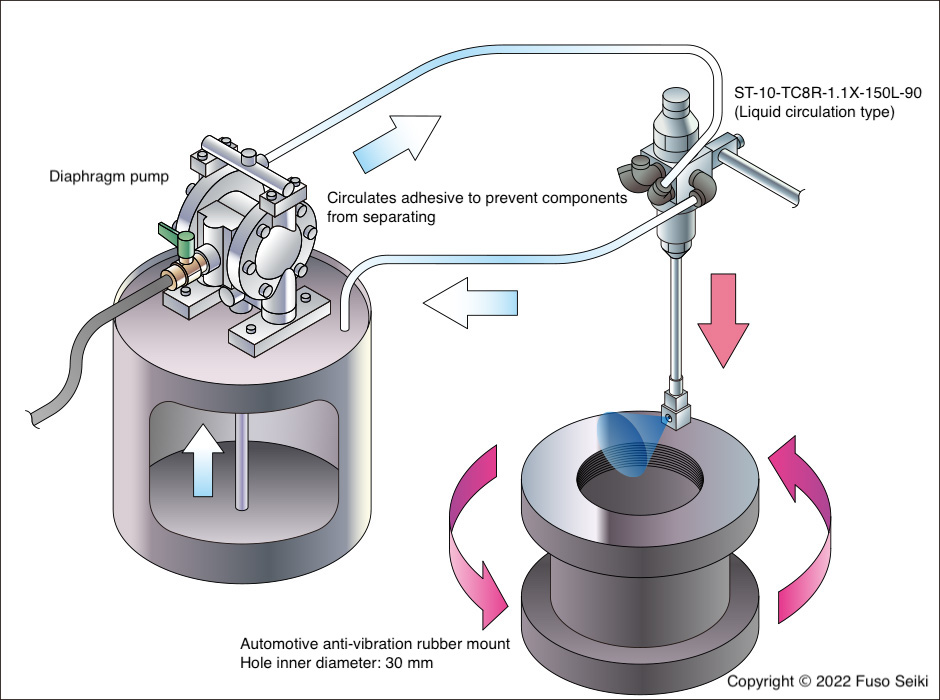
Lumina’s proposal and result
We introduced the C8 series with its small 7-9 mm square head, which is effective for coating the insides of small holes. In this case, we chose a customized TC8 nozzle with a disposable liquid tube as the liquid is an adhesive that tends to clog. The liquid tube for the standard C8 nozzle is made of stainless steel and is integrated with the outer air tube. On the other hand, the liquid tube for the TC8 is a replaceable PTFE tube.
The C8/TC8 offers flat-fan and round spray patterns. Although flat-fan spraying is sometimes used in cases similar to this, we chose round spraying (90-degree round spraying) for this project because of the simple structure and stable spraying.
To prevent sedimentation and separation of adhesive components, we decided to use a diaphragm pump to circulate the liquid. For this reason, we adopted the ST-10 model, a circulation-compatible model, for the body of the spray gun.
- (Spraying conditions)
-
- Atomizing air pressure: 0.1 MPa
- Liquid supply: Diaphragm pump
- Target distance: 15 mm
By rotating the workpiece (object) and spraying while lifting the C8 head inserted into the hole, the adhesive could be evenly applied to the entire inside of the hole. Since the small C8 head is prone to clogging, it is frequently cleaned during operation (see the following technical column for information on how to prevent clogging of the spray gun: What to Do if Your Spray Gun Clogs).
Example 2
- User
- Major textile processing manufacturer
- Application
- Adhering interior finish materials for automobiles
- Model used
- PR-40-2.0X
Problem
This manufacturer uses a press process to attach interior finish materials for automobiles together using an adhesive (with a viscosity of 350 mPa·s at 25 degrees Celsius).
They had already tried various automatic spray guns in the past, but they were encountering various problems. For example, the adhesive was drying up into threads midair during spraying, their spray coverage was not wide enough, and overspray was causing the area around the spray gun to get dirty.
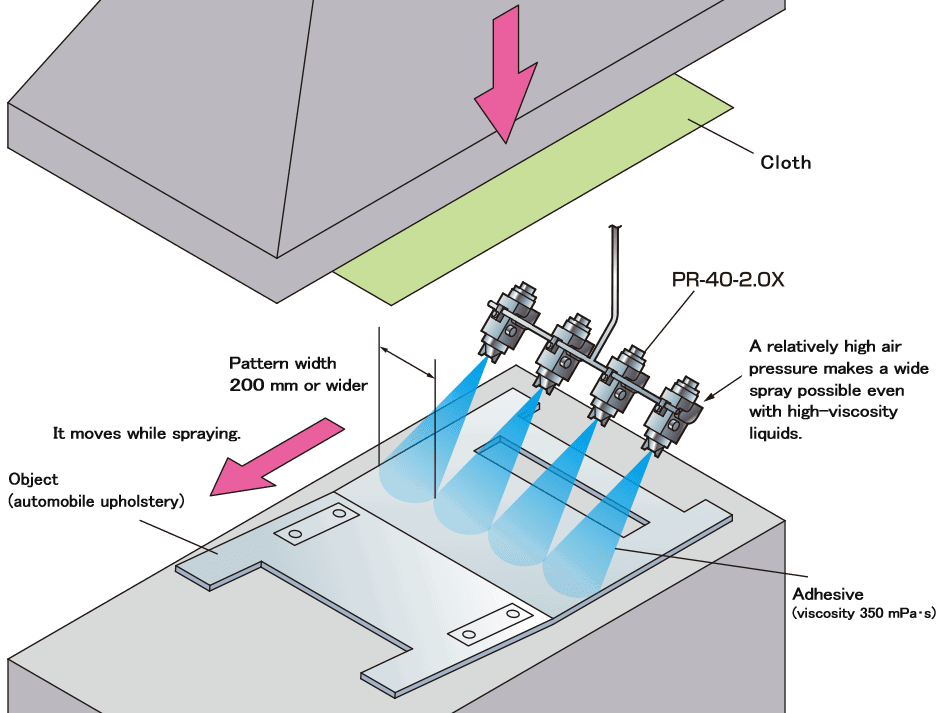
Lumina’s proposal and result
We proposed the PR-40, which is our model with the widest spraying capability. The PR-40 features two adjusters – one for atomizing air pressure and one for pattern air pressure – so its mist can be fine-tuned. For this application, the atomizing air pressure was set relatively low for an adhesive to prevent overspray, while
the pattern air pressure was set high to ensure the spray pattern was wide enough.
- (Spraying conditions)
-
- Atomizing air pressure: Approximately 0.08 to 0.18 MPa
- Pattern air pressure: Approximately 0.15 to 0.25 MPa
- Liquid pressure: 0.15 MPa (using pressure feed tank)
- Target distance: 300 mm
As a result, the PR-40 pattern width was increased by 30% to 40% compared to their old spray gun, allowing them to coat an area over 200 mm wide with a single spray gun.
We also solved the issue of the adhesive partially drying in midair, and by setting the atomizing air pressure relatively low, overspray was no longer an issue, greatly improving the work environment.
Example 3
- User
- Automobile parts manufacturer
- Application
- Applying adhesive
- Model used
- ST-5R-0.5X
Problem
This manufacturer attaches rubber seals to 0.8 mm steel plates with adhesive to manufacture automobile window frame materials. They were looking for a way to efficiently coat each of the three sides of the object with adhesive.
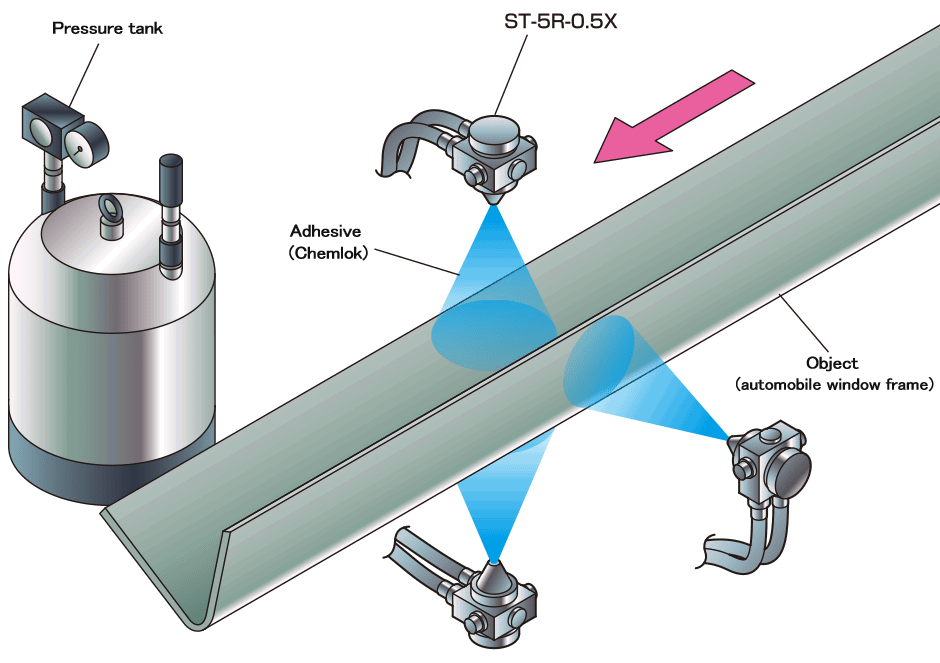
Lumina’s proposal and result
We proposed three ST-5R-0.5Xs with round spray patterns. To handle the adhesive viscosity, we suggested a relatively high atomizing air pressure. Pressure feed tanks were used to convey the liquid.
- (Spraying conditions)
-
- Atomizing air pressure: 0.22 MPa
- Liquid pressure: 0.3 MPa (using pressure feed tank)
- Liquid flow rate: 10 mL /min
As a result, we succeeded in creating a system to provide adhesive as the client envisioned. With just periodic maintenance, their system now has a stable performance with fewer clogs.