Introduction to MQL Lubrication for Machining/Cutting
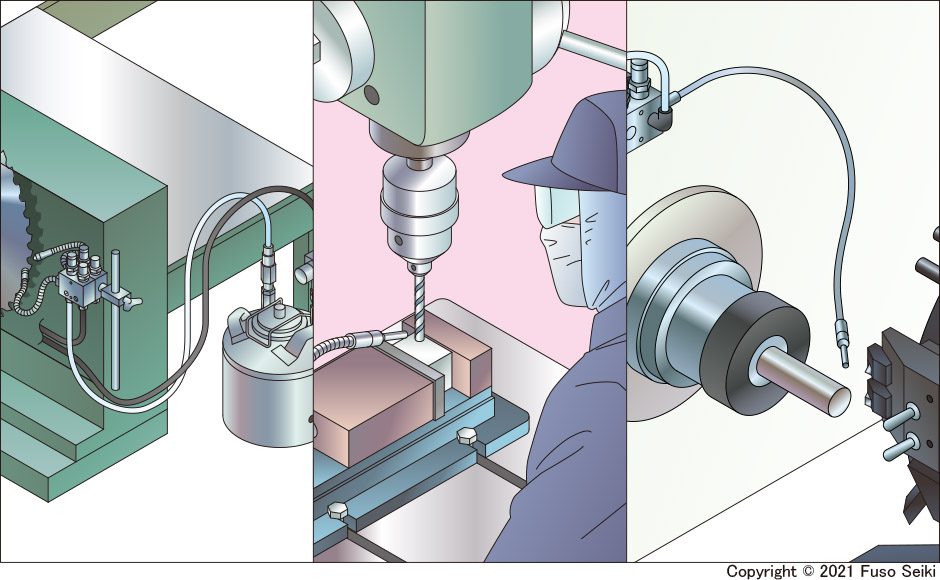
Cutting fluid is indispensable in machining/cutting metal. Apart from the main stream of flood coolant, there is a low-cost and easy method, which is a Minimum Quantity Lubrication (MQL) system that sprays out minute amounts of cutting fluid as a cold mist. In this column, the basic features of MQL (near-dry machining) and its main uses will be explained.
Is flood coolant really the best way to provide lubrication?
In machining and cutting aluminum, steel, and stainless steel, etc., lubrication is a necessary part of machining centers, CNC lathes, and manual processing tools such as band saws and drilling machines. Lubrication reduces frictional resistance during machining/cutting, cools the blade, and carries off hot chips/shavings. These three functions of lubrication prevent the precision of the work from being degraded by the heat of processing and extends the life of tools.
The first source of lubrication that comes to mind when machining/cutting is the flood coolant nozzle used in machining centers and with CNC lathes. The polyacetal hose and the nozzle are connected, and then cutting fluid pours towards the cutting zone. Additionally, some of these automatic machines are equipped with a high-pressure coolant device (Through-Spindle Coolant) that has coolant jet out directly from a pair of holes in the tool.
Easy and low-cost MQL
However, these devices cannot be used on engine lathes, drilling machines, or cutting machines where the machine is not fully covered. Furthermore, even when processing with an automatic machine, aluminum and brass materials do not release significant amounts of heat, so a simpler method may be sufficient.
Minimum quantity lubrication (MQL) is the third option for such use cases. This is a lubrication method in which a minute amount of cutting fluid, approx. 5 to 60 mL per hour, is turned into a mist and sprayed onto the cutting edge/tooltip. The finely atomized cutting fluid particles instantly evaporate when they come into contact with the hot tool, and, in doing so, they carry away heat and cool the tool (this is called the heat of vaporization). Additionally, due to the force of the air, this mist blows away the chips/shavings that are generated during processing. It enables low-cost, hassle-free machining that is as close to being dry (no lubrication) as possible.
Bidirectional types can be used to lubricate both sides of the blades
Now then, let’s take a look at some use cases for Lumina’s “Magic Cut” MQL device.
This is an example of attaching Magic Cut to a metal cutting machine. A mounting rod is erected in the box where the circular saw (metal saw) returns after cutting, and a bidirectional (two linked units) Magic Cut is fixed in place.
When a large amount of frictional heat is generated from cutting a plate or pipe, hot chips/shavings become welded to the cutting edge and its sharpness deteriorates. This may cause blade chipping or injury if it is used as is, so it is necessary to lubricate and cool the cutting edge.
The main body of the Magic Cut (the atomizer) is compact, with dimensions of just 50mm x 20mm x 40mm (length x width x height), so it can even be installed in cramped and narrow spaces. If a bidirectional Magic Cut is used, then cutting fluid can be applied to both sides of the blade. Spray timing is controlled feeding a signal taken from the cutting machine into the solenoid valve to turn the air on and off.
Cutting plates or pipes does not generate as much heat as machining, and as such, with MQL you can handle not just aluminum, but also hard materials such as stainless steel and titanium.
Proven track record for lubricating band saws
Band-saw type cutting machines are also often used for cutting. These are machines that have a high blade rotation speed, produce a beautifully cut surface, and are often used for cutting steel pipes, stainless steel pipes, round bars, and aluminum window frames, etc. In the above example, a Magic Cut is attached directly to the side of the cutting machine with a magnet, and the nozzle at the tip is facing the cutting edge, with the spray timing controlled by the foot pedal.
Some people may be concerned that spraying cutting fluid in a location with nearby workers will cause the workers to inhale it, so in these cases an oil mist collector can be used together with the Magic Cut unit. However, Magic Cut is an MQL device that atomizes and sprays minute quantities of cutting fluid, so only a very small quantity is released into the atmosphere unless it is continuously sprayed.
Additionally, Magic Cut offers optional air caps (air nozzles) for different applications. The standard air nozzle is intended to be used with a small amount of cutting fluid and high air pressure so that it can cool and remove chips/shavings. However, if you prioritize lubricating the cutting edge/tooltip, then the optional short air nozzle is recommended. The short air nozzle can cleanly and softly spray, even with a larger amount of cutting fluid and low air pressure, so scattering of cutting fluid can be minimized. The above illustration also uses the short air nozzle.
Switching from brush-based coating provides efficiency improvements
Magic Cut is also often used when machining with drilling machines and placing screws with tapping machines. In conventional brush applications, workers engage in a multi-step process of machining, applying cutting fluid with a brush, setting the brush down, placing the next work piece, and then finally machining again. However, when a Magic Cut is linked to a foot pedal, the brush-related steps can be completely removed and cutting fluid can be directly applied to the tool via the foot pedal, greatly increasing productivity. There are two types of taps, rolling taps and cutting taps, and the advantage of Magic Cut is that it can also remove the chips/shavings produced by cutting taps.
Ultra-precision machining is a specialty of MQL
Of course, CNC lathing and face milling also uses Magic Cut. Magic Cut is suitable for processing aluminum and brass materials that give off low amounts of heat when processed (be careful not to affix the Magic Cut in a position where it will be bumped into, as the turret, etc. will move during processing).
In addition, ultra-precise machining, at the micrometer and nanometer scale, is an area that MQL excels at because these types of ultra-precise machining are slow and don’t generate large amounts of heat, and Magic Cut has a high track record of adoption. Attaching the short air nozzle enables clean atomization of cutting fluid with low volumes of air.
As mentioned previously, Magic Cut has a variety of optional air nozzles, line nozzles, and peripherals to meet different applications and usage conditions, so please refer to the catalog if you would like to learn more, and please feel free to contact us if you have any questions.